

Process Control… RFID Has It Under Control
Written by: Rick Raber, CTO - Northern Apex Corporation
Data reporting can be a very tedious process for source medical device manufacturers. The functionality of the device needs to be spot-on for it to be considered viable in the medical community. Because there is little to no room for error in this process, medical devices must help decrease error prone manufacturing activities, and in many cases also help companies meet the desired Six Sigma goal for process control. Radio Frequency Identification (RFID) is a technology that when deployed properly can help companies address process critical shortcomings. RFID is considered as the ‘next generation’ improvement over standard barcode labels. RFID does not require direct line of sight as compared to barcode. RFID labels/tags simply need to be within a specific range of a reader/antenna to report its serial number and other information. This technology has another added advantage - the tag contains a tiny microchip that allows it to store, carry and transmit data, making it a portable micro-storage device for remote data access. While RFID is not a complete replacement for barcode labels, these inherent technical features make RFID the appropriate choice to address data recovery and Six Sigma in life science applications.
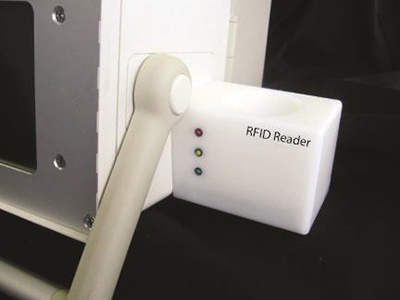
Example of RFID enabled label
RFID delivered real-time information about product performance and fluid identification.
Overview:
An international lab equipment manufacturing company was looking for a way to ensure that calibration data from their consumable items was accurately being reported in the production process. RFID became the choice technology to meet plan objectives. Integrating RFID technology into products that are designed for use in the manufacturing of biopharmaceuticals became the goal. The scope of this project was to design and manufacture a device with the specification and criteria that would result in a unit with acceptable operator interface, computing platform, tag reader/antenna design and meet the required traceability parameters that the industry expects and requires. The final goal of the device was to give the equipment manufacturing company’s customers the ability to quickly and accurately identify the product’s critical parameters used in biopharmaceutical manufacturing, while also enhancing their ability to meet FDA requirements.
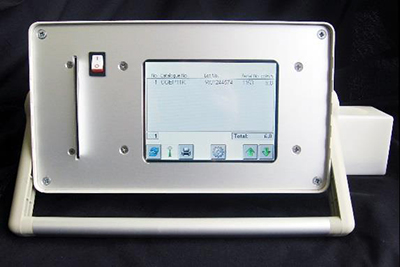
Final Validation Device
Solution:
Device Specification
Utilizing an RFID integrator, the manufacturing company began the initial steps of incorporating RFID into their products. A step-by-step overview of the specifications for the product was created, as well as enclosure selection, and mechanical configuration. Given the close proximity of the device to the RFID reader and materials, the RFID integrator decided that a 13.56 MHz RFID frequency works best for this type of device; this was due to the required limited read range of the tags, as well as the RFID reader/tag’s ability to operate when placed near liquids. The device needed a color touchscreen display for operator interface, a printer to provide the customer with a printed copy of the device’s parameters for traceability data, and a microcontroller based software system for a less complex, quick running and cost-effective operation. The RFID integrator took the design specifications and utilizing their engineering and manufacturing departments, sourced the components and created an initial 3D CAD drawing of the device. After the design and prototype phases were complete, the instrument was sent to the FCC for testing and approval.
Device Function/Use
The net result is a smart RFID device that functions as a process control and traceability system for pharmaceutical manufacturers. During manufacturing line validation, pharmaceutical companies can rest assured that the critical component information is stored directly on the tag embedded in the products. The end customer uses the device to capture the critical data from each tag used in a production run. It then compiles the information into a traceability report that prints on the device’s printer.
The device allows its users to automatically document product and process information, which provides the necessary industry specific traceability information. It also increases speed and reliability when retrieving critical item based performance criteria, for example the reporting of when and how the product was manufactured.

Sample Screen Reading
Summary:
By using RFID technology to drive process critical data embedded in the product, the lab device equipment manufacturer’s customers increased their speed and accuracy by quickly and reliably retrieving critical process information. Additionally, when the device was combined with existing live validation procedures, RFID delivered real-time information about product performance and fluid identification during the end client’s manufacturing process. The information obtained helped their customers guarantee regulatory compliance and made the recording and conveying of manufacturing data much faster and more reliable.